Alcast Company - Truths
Alcast Company - Truths
Blog Article
Alcast Company for Dummies
Table of ContentsExcitement About Alcast CompanyAlcast Company Things To Know Before You BuyThe Ultimate Guide To Alcast CompanyThe Alcast Company PDFsAlcast Company Fundamentals ExplainedFacts About Alcast Company Revealed
The subtle distinction exists in the chemical web content. Chemical Contrast of Cast Light weight aluminum Alloys Silicon advertises castability by reducing the alloy's melting temperature level and enhancing fluidity during casting. It plays a critical role in allowing detailed mold and mildews to be filled up accurately. In addition, silicon adds to the alloy's strength and use resistance, making it valuable in applications where resilience is important, such as automotive components and engine elements.It likewise boosts the machinability of the alloy, making it easier to process right into ended up items. In this method, iron adds to the general workability of aluminum alloys.
Manganese adds to the stamina of light weight aluminum alloys and improves workability (Casting Foundry). It is frequently used in functioned light weight aluminum products like sheets, extrusions, and accounts. The visibility of manganese aids in the alloy's formability and resistance to fracturing throughout fabrication procedures. Magnesium is a light-weight element that provides stamina and effect resistance to light weight aluminum alloys.
A Biased View of Alcast Company
Zinc boosts the castability of aluminum alloys and aids control the solidification process during casting. It boosts the alloy's stamina and firmness.
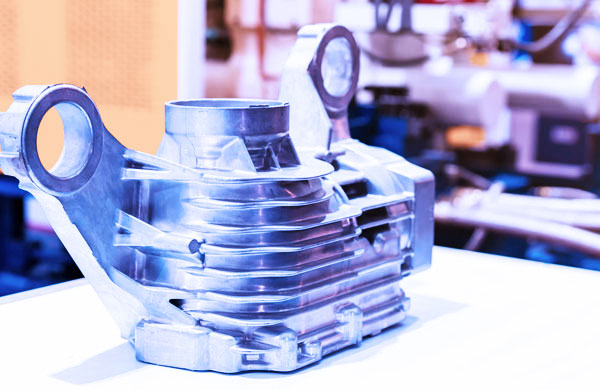
The main thermal conductivity, tensile stamina, yield toughness, and prolongation differ. Amongst the above alloys, A356 has the highest possible thermal conductivity, and A380 and ADC12 have the cheapest.
The Single Strategy To Use For Alcast Company
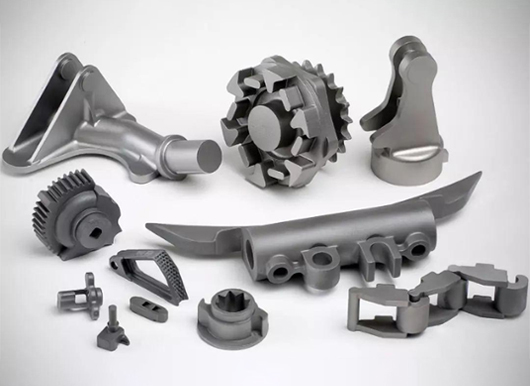
In accuracy casting, 6063 is fit for applications where intricate geometries and high-grade surface coatings are critical. Examples include telecommunication units, where the alloy's remarkable formability permits for sleek and visually pleasing designs while maintaining structural integrity. In the Lighting Solutions industry, precision-cast 6063 parts develop elegant and effective lights components that require complex shapes and great thermal efficiency.
It results in a better surface area finish and much better corrosion resistance in A360. The A360 displays premium prolongation, making it perfect for facility and thin-walled components. In accuracy spreading applications, A360 is appropriate for sectors such as Customer Electronic Devices, Telecommunication, and Power Devices. Its boosted fluidness allows for detailed, high-precision parts like smartphone casings and communication device housings.
The Best Guide To Alcast Company
Its one-of-a-kind residential or commercial properties make A360 a useful choice for precision casting in these sectors, enhancing product toughness and top quality. Light weight aluminum alloy 380, or A380, is a widely used casting alloy with a number of distinctive attributes. It uses excellent castability, making it a perfect choice for precision casting. A380 displays excellent fluidity when molten, making sure complex and in-depth mold and mildews are accurately duplicated.
In accuracy casting, aluminum 413 beams in the Consumer Electronics and Power Devices industries. It's typically utilized to craft intricate parts like mobile phone housings, cam bodies, and power device casings. Its precision is amazing, with limited resistances approximately 0.01 mm, making sure flawless product setting up. This alloy's remarkable corrosion resistance makes it an excellent option for exterior applications, making sure lasting, resilient products in the pointed out sectors.
Everything about Alcast Company
The light weight aluminum alloy you select will considerably affect both the casting procedure and the homes of the final product. Due to the fact find here that of this, you must make your decision thoroughly and take an informed strategy.
Identifying the most ideal aluminum alloy for your application will imply weighing a large range of characteristics. These relative alloy attributes adhere to the North American Pass Away Casting Organization's guidelines, and we've split them right into two categories. The first classification addresses alloy features that influence the production process. The 2nd covers characteristics influencing the residential or commercial properties of the end product.
See This Report on Alcast Company
The alloy you select for die casting straight influences a number of elements of the spreading process, like exactly how very easy the alloy is to deal with and if it is prone to casting issues. Warm cracking, additionally understood as solidification fracturing, is a common die casting defect for light weight aluminum alloys that can cause inner or surface-level tears or fractures.
Particular aluminum alloys are more at risk to warm cracking than others, and your choice must consider this. One more usual problem discovered in the die casting of aluminum is die soldering, which is when the cast sticks to the die walls and makes ejection tough. It can harm both the actors and the die, so you must look for alloys with high anti-soldering residential or commercial properties.
Deterioration resistance, which is currently a notable characteristic of aluminum, can differ substantially from alloy to alloy and is an essential particular to consider relying on the ecological problems your product will be revealed to (Foundry). Wear resistance is another property commonly looked for in light weight aluminum items and can differentiate some alloys
Report this page